УДК691.51.66.046.4
Исследование влияния формы и направленности факела на эффективность работы вращающейся печи для обжига каолина на шамот.
Троценко Л.Н., канд. техн. наук, Пикашов В.С., канд. техн. наук., Стративнов Е.В. канд. техн. наук, Правило С.В., Виноградова Т.В.
Институт газа НАН Украины, Киев
ул. Дегтяревская, 39, 03113 Киев, Украина, e-mail: t-ln@ukr.net
В Институте газа НАН Украины разработана и внедрена на вращающейся печи для обжига каолина комбината по производству огнеупоров новая система отопления на базе двухпроводной газовой горелки с регулируемой длиной факела мощностью 35 МВт и максимальным расходом природного газа 4000 м3/ч. В горелку подается первичный воздух в количестве 25–30 % от всего необходимого для полного сжигания воздуха. Вторичный воздух подается через холодильник шамотной крошки за счет тяги печи, нагреваясь до температуры 500–700 °С. Температура в зоне обжига 1450–1500 °С.
Горелка дает возможность регулировать длину факела и тем самым обеспечивать требуемое технологией распределение температуры по длине печи. Регулирование длины факела в горелке осуществляется с помощью газового клапана с конусным наконечником с отверстиями, который может перемещаться вдоль оси горелки и частично или полностью перекрывать основное центральное отверстие газового сопла. Подача газа распределяется между центральным и боковыми отверстиями, создавая различные условия для перемешивания топлива и воздуха. Отличительной особенностью горелки является наличие стабилизатора горения, установленного в воздушном зазоре.
В систему отопления входит защитно-запальное устройство (ЗЗУ), система безопасности и регулирования температуры в печи. Для регулирования температуры в зоне обжига вращательных печей во внутренних слоях кладки были установлены термодатчики с бесконтактной передачей сигнала к пульту управления при помощи радиомодема, работающего на солнечных батареях.
Проведены сравнительные исследования влияния размера, формы и направленности факела на теплообмен в печи, в результате которых установлены оптимальные размеры факела, угол наклона его оси к оси печи и как следствие его направленность по отношению к поверхности нагреваемого материала. После настройки печи на оптимальные режимы работы достигнуты следующие показатели: коэффициент расхода воздуха a снизился с 1,1–1,3 до 1,05–1,1; уменьшено разрежение перед дымососом от 1,2–1,5 до 0,8–1,0 кПа, расход природного газа снижен при непрерывной работе печи на 30 %, а среднегодовая экономия топлива составила 15 %.
Ключевые слова: вращающаяся печь, система отопления, параметры факела, теплообмен, кладка.
Вращающиеся печи благодаря своим преимуществам по сравнению с другими конструкциями печей для термохимической обработки сыпучих материалов широко распространены в различных отраслях промышленности. Это предприятия цветной и черной металлургии, химической промышленности, производства цемента и других строительных материалов и др. Такие печи работают по принципу противотока. Со стороны загрузки в рабочее пространство подается обжигаемый материал, а со стороны выгрузки непрерывно подаются горячие продукты сгорания топлива, которые движутся навстречу медленно сползающему и пересыпающемуся вниз материалу, нагревают его, испаряя содержащуюся в нем влагу, и далее нагревают его до заданной температуры, способствуя протеканию термохимических реакций. После тепловой обработки материал поступает на дальнейшую переработку или в холодильник.
В зависимости от требований технологии в процессе обжига или сушки, состава обрабатываемого сырья, производительности печи, скорости вращения печи необходимо обеспечить строго определенное распределение температур по ее длине. Причем, на одном и том же агрегате режимы термической обработки материала могут изменяться в зависимости от состава сырья, его влажности, размера фракции и т.п., что требует оперативного регулирования температурного распределения вдоль печи. Часто на практике управление тепловым режимом и определение его оптимального значения осуществляется несколькими способами [1]: изменением тепловой мощности (расхода топлива); регулированием коэффициента расхода воздуха, когда за счет энергии избыточного воздуха перемещают зону высоких температур; изменением положения горелки с наклоном на материал; регулированием разрежения в головке печи и режима работы холодильника. В большинстве случаев это приводит к ощутимому изменению технологических параметров работы печи и неэффективности ее работы в целом.
Проведено большое количество теоретических, экспериментальных и промышленных исследований работы вращающихся печей, обобщенных в работах [1, 2, 3] и других. Основной целью исследований являлось экономное использование энергоресурсов и повышение качества продукта, что связано с поиском оптимальных параметров теплового режима работы печей. В свою очередь одним из важных направлений оптимизации работы печей является интенсификация теплообмена в рабочем пространстве. В данной статье рассматривается влияние размера и направленности факела в рабочем пространстве на эффективность работы печи в целом.
Принято считать, что нагрев материала на 70–90 % происходит непосредственно излучением от факела и переизлучением от кладки на открытую поверхность материала [1, 3]. В других источниках согласно теоретическим расчетам получено, что тепловой поток от разогретой кладки к материалу за время контакта материала с кладкой может превышать поток тепла через открытую поверхность материала более, чем в три раза [2]. Эти расчеты подвергаются критике и предполагается, что в реальных условиях часть теплоты, переданной от кладки материалу при их непосредственном контакте, может быть не более 10–30 % от всего тепла, переданного материалу. При этом многие исследователи считают, что наиболее интенсивный нагрев материала осуществляется при направлении факела и потока продуктов сгорания непосредственно на материал [1, 2]. Это справедливо лишь для некоторых случаев, когда качество обожженного материала не ограничивается максимальной температурой на его поверхности и когда слой материала термически тонкий.
В действительности во вращающихся печах обрабатываются сыпучие материалы с различными теплофизическими свойствами. Толщина нагреваемого слоя переменна, так как часто пересыпается только часть материала у свободной поверхности, а остальной материал, образуя плотное ядро внутри насыпной массы, скользит по кладке и не имеет поверхности, контактирующей с факелом и продуктами сгорания. Кроме того установлено [4, 5], что профиль сыпучего материала во вращающемся барабане формируется, начиная с разгрузочного конца и свободная поверхность сыпучего материала выпуклая. В связи с этим представляют интерес практические исследования влияния геометрических характеристик и направленности факела, а также роли кладки в теплообмене вращающихся печей.
Рассматриваемая печь для обжига каолина на шамот с длиной и диаметром барабана 75 и 3,6 м соответственно имела следующую систему отопления. В торцевой стене откатной головки печи на горизонтальной оси барабана были установлены две горелки в виде труб, оканчивающихся соплами, над которыми по вертикальной оси печи была расположена труба для подачи первичного воздуха (рис1а). Производительность печи составляла 20–22 т/ч; рабочая температура в зоне обжига печи 1450–1500 °С. Номиальный расход газа на печь составлял 3000–3500 нм3/ч; количество первичного воздуха, подаваемого в воздушную трубу, составляло 25–30 % от всего воздуха, участвующего в горении. Подача вторичного воздуха, проходящего через холодильник и нагревающегося до температуры 500–700 ºС, осуществлялась за счет разрежения в печи.
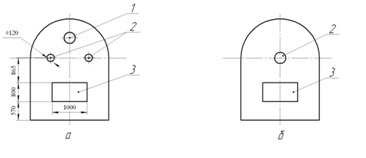
Рис.1. Схема установки горелок и воздушной трубы на лицевой стороне откатной головки печи до и после реконструкции.
1 — место установки воздушной трубы для подачи первичного воздуха; 2 — места установки горелок; 3 — технологическое окно.
Нами были проведены компьютерные исследования (CFD) скоростных и концентрационных характеристик холодных газовых потоков во вращающейся печи. На рис. 2 проиллюстрированы картины течения печных газов для трех вариантов подачи газа и первичного воздуха.
 |
Вариант 1 |
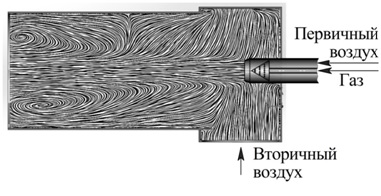 |
Вариант 2 |
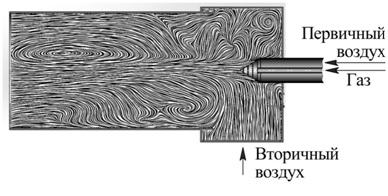 |
Вариант 3 |
Рис. 2. Линии течения печных газов для различных вариантов подачи топлива и воздуха
Вариант № 1соответствует существовавшей системе отопления исследуемой печи (рис. 2а). Вариант № 2 – расположению двухпроводной горелки по оси печи с истечением газа через центральное сопло. Вариант № 3 – то же с истечением газа отдельными струями под углом 45° к потоку первичного воздуха. Распределение воздуха для горения на первичный и вторичный во всех вариантах в соответствии с характеристиками печи. При этом в вариантах 2 и 3 первичный воздух подавался в горелку, а расход вторичного воздуха на горение сохранялся в том же количестве, что и на существующей печи. При расчетах принимали, что средой является смесь природного газа и воздуха при температуре 20 ºС. Вращение печи (1,0…1,5 об/мин) и наклон корпуса печи в расчетах не учитывали ввиду малости компонента окружной скорости (менее 0,2 м/с) и угла наклона (3º) корпуса печи.
На представленном рисунке, соответствующему варианту 1, видно, что поток первичного холодного воздуха идет параллельно газу. Перемешивание газа и воздуха на начальном участке не происходит, за исключением подсоса печных газов к корню факела. Это приводит к затягиванию горения, охлаждению стенок цилиндрической камеры и перемещению зоны высоких температур к загрузочному краю барабана. Очевидно, что при этом также температура и, следовательно, интенсивность теплообмена в зоне обжига низкая, что приводит к перерасходу топлива и ухудшению качества продукции.
На рисунках, соответствующих вариантам 2 и 3, представлены крайние случаи подачи топлива и воздуха в горелку: при истечении газа через центральное сопло (вариант 2) получается самый длинный факел, расположенный в осевой части рабочего пространства; при истечении газа отдельными струями под углом к потоку воздуха (вариант 3) получается короткий и объемный факел, что обеспечивает равномерное поле температур в поперечном сечении барабана. Промежуточные положения не представлены ввиду нецелесообразности в рамках представленных исследований.
Ввиду того, что внутреннее пространство печи не осесимметрично, а также имеет место подсос вторичного воздуха в нижней части печи, представляет определённый интерес 3-D изображения нижнего и верхнего предела концентрации метана в объёме печи (см. рис. 3) для трёх вариантов исполнения топливосжигающих устройств. Синим цветом показана нижняя граница концентрации, соответствующая максимальному избытку воздуха (альфа 1,2), красным цветом - соответственно верхняя. Приведенная на объемных эпюрах информация соответствует начальному (до начала горения) расположению необходимой для поджога горючей смеси. Таким образом, она может быть использована для выбора формы и направленности факела.
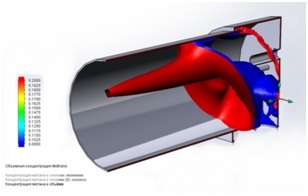 |
Вариант 1 |
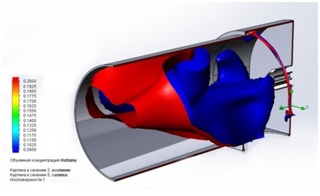 |
Вариант 2 |
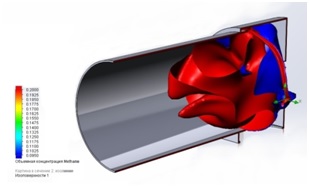 |
Вариант 3 |
Рис. 3. Концентрация метана в объеме печи
Можно предположить, что при изменении положения факела между его крайними положениями на промышленной печи можно добиться не только равномерных тепловых потоков на кладку и свободную поверхность шихты, но и регулировать длину высокотемпературной зоны печи.
Для обеспечения эффективной работы вращающихся печей за счет управления их температурным режимом Институтом газа НАН Украины была разработана горелка с регулируемыми параметрами факела, в основу конструкции которой положены известные принципы регулирования интенсивности смешения газа и воздуха [3, 6], Горелка относится к типу диффузионных, когда горение газа происходит по мере его перемешивания с воздухом в рабочем пространстве. Отличительной особенностью горелки является наличие стабилизатора горения в виде плохо обтекаемого тела, установленного в воздушном кольцевом зазоре [7]. Установка горелки предполагалась по оси печи (рис. 1б).
На рисунке 4 показана установка горелки на печи взамен двух существовавших горелок. Горелка была установлена в торце откатной головки по оси барабана с возможностью перемещения ее внутрь печи и наклона ее относительно оси печи.
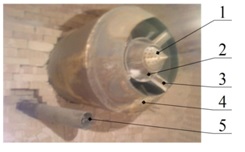
Рис.4. Установка горелки ПГ-35М в комплекте с ЗЗУ. Вид из рабочего пространства.
1 — конусная часть газораспределительного клапана с отверстиями для истечения газа; 2 — центральное газовое сопло; 3 — стабилизатор; 4 — воздушное сопло; 5 — ЗЗУ.
Горелка состоит из воздушного цилиндрического корпуса, оканчивающегося конусом в виде сопла. Внутри воздушного корпуса расположена наружная и внутренняя газовые трубы, оканчивающиеся газовым соплом. Регулирование длины факела горелки ПГ-35М осуществляется подвижным газораспределительным клапаном, состоящим из цилиндрической полой части и полого конуса со стороны сопловой части горелки. На цилиндрической части выфрезерованы продольные пазы для прохода газа, а в конусе высверлены отверстия для истечения газа. Газораспределительный клапан перемещается в продольном направлении с помощью маховика. Регулируя положение клапана, можно создавать различные условия для истечения газа: сплошной струей через центральное отверстие горелки или отдельными струями через боковые отверстия, направленные под углом к воздушному потоку, тем самым изменяя длину факела между его крайними значениями от 5 до 25 м. Наличие компенсаторов на подводящих воздухо- и газопроводах дает возможность регулировать наклон горелки относительно оси печи до 5°.
Автоматизация системы отопления печи была выполнена на основе блока управления БАУ-ТП (микропроцессорного контролера с индивидуальным программным обеспечением) и стандартных датчиков. Необходимые элементы автоматики безопасности и регулирования были размещены на подводящем газопроводе на газовой рампе, которая размещена непосредственно у горелки. Благодаря непрерывному контролю давления газа и воздуха на горение, наличия пламени на ЗЗУ и разрежения в печи обеспечивалась надежность и безопасность работы всей системы. В систему регулирования тепловым режимом печи был включен контроль температуры кладки зоны обжига от трех термодатчиков. Сигналы о температуре внутренних слоев кладки зоны обжига в трех точках по ее длине передавались к пульту управления при помощи радиомодема, работающего на солнечных батареях. Показания этих термодатчиков учитывались операторами печи для регулирования тепловой мощности горелки ПГ-35М и установки оптимальной длины факела.
Промышленные эксперименты по определению оптимальных параметров работы новой системы отопления проводились в течение нескольких месяцев. Поскольку непосредственные измерения длины факела, его температуры и параметров теплообмена внутри печи практически невозможны, о работе системы отопления судили визуально через гляделки, по показаниям установленных в зоне обжига термопар, входным и выходным параметрам работы печи, а также исходя из сравнительного анализа результатов компьютерных исследований (рис. 2, 3) на основе законов аэродинамики и горения.
Проведен комплекс исследований с целью выбора оптимального режима работы печи при различных геометрических и режимных параметрах настройки горелки ПГ-35М. Изменялись углы наклона оси горелки по отношению к оси печи в пределах 5° в различные стороны при перемещении газового клапана в промежуточные положения. Все опыты проводились при постоянной максимальной производительности печи и переменной тепловой мощности. Параллельно проводили анализ дымовых газов, определение качества продукции и других показателей (табл. 1).
Таблица 1.
Результаты промышленных испытаний работы вращающейся печи до и после установки новых горелок
№
|
Параметры
|
Размерность
|
До реконструкции
|
После реконструкции
|
1
|
Производительность печи
|
т/ч
|
19–23
|
18–23
|
2
|
Давление природного газа перед
горелками
|
кПа (кгс/см2)
|
80
(0,8)
|
80
(0,8)
|
3
|
Расход природного газа
|
м3/ч
|
3100
|
2200
|
4
|
Давление первичного воздуха
|
кгс/м2
|
200–220
|
200–220
|
5
|
Расход первичного воздуха
|
м3/ч
|
9000–11000
|
6000–8000
|
6
|
Температура в горячей головке печи
|
°С
|
660–750
|
760–860
|
7
|
Температура в пылевой камере
|
°С
|
420–550
|
330–360
|
8
|
Температура перед электрофильтрами
|
°С
|
250–280
|
180–190
|
9
|
Температура перед дымососом
|
°С
|
100–150
|
80–90
|
10
|
Разрежение в горячей головке печи
|
кгс/м2
|
1,0–2,0
|
1,0–2,0
|
11
|
Разрежение в пылевой камере
|
кгс/м2
|
5,0–7,0
|
3,0–4,0
|
12
|
Разрежение перед дымососом
|
кгс/м2
|
120–150
|
80–100
|
Результаты исследований показали, что оптимум по удельным расходам топлива на единицу продукции и максимальному качеству шамота были получены при наклоне горелки относительно оси печи на 5° в сторону футеровки, противоположную поверхности насыпного материала и при расположении среза сопла горелки вблизи торцевой стенки откатной головки. При этом газовый клапан находился в среднем положении. Последнее можно объяснить тем, что при длинном факеле значительно растягивается зона горения, а при коротком пламени факел был объемным, перегревая входную часть печи.
Новая система отопления находится в эксплуатации более 6 лет. Ее внедрение позволило упростить управление тепловым режимом печи и улучшить основные показатели тепловой работы. За счет улучшения условий смешения газа и воздуха в горелке удалось снизить количество холодного первичного воздуха без изменения параметров вторичного воздуха. В результате коэффициент расхода воздуха a снизился с 1,1–1,3 до 1,05–1,1; догорание топлива за пределами рабочего пространства практически отсутствовало, что является свидетельством снижения химического недожога газа и создания нормальных условий для работы вспомогательного оборудования. Температура газов на выходе из печи уменьшилась на 100–200 °С, что свидетельствует об интенсификации теплообмена в рабочем пространстве и уменьшении потерь тепла из рабочей зоны с продуктами сгорания. Снижение температуры и количества отходящих газов перед электрофильтрами и дымососом также положительно сказалось на условия их работы.
Улучшились экологические показатели работы печи. Благодаря уменьшению разрежения перед дымососом от 1,2–1,5 до 0,8–1,0 кПа в печи с новой системой отопления значительно снизился пылеунос, а приведенные к a = 1,0 выход NОх после печи составлял не более 225 мг/м3 и СО – 0,019 % об. по данным государственных испытаний, что соответствует принятым в Украине нормам по вредным выбросам в окружающее пространство.
Выводы.
- Благодаря конструкции горелки ПГ-35М и ее креплению на печи появилась возможность регулировать геометрические и режимные параметры факела и, в результате, исследовать различные режимы горения и теплообмена для выбора оптимального режима работы печи.
- Показана роль кладки в эффективности нагрева материала применительно к конкретной технологии обжига каолина на шамот. Проведенные исследования и настройка работы системы отопления на оптимальный режим дает возможность точного соблюдения технологических требований, а именно, заданного распределения температур по длине печи. Обеспечение оптимального температурного поля в зоне обжига позволяет сократить удельные затраты топлива на получение шамота без ухудшения его качества. Экономия топлива в рабочем режиме без простоев достигала 30 %, а среднегодовая экономия природного газа составила 15–20 %.
- Следует отметить, что полученные результаты исследований не всегда применимы для других материалов, технологий и систем отопления вращающихся печей.
Список литературы.
- Лисиенко В.Г., Щелоков Я.М., Ладыгичев М.Г. Вращающиеся печи: теплотехника, управление и экология/ Справочное издание. Книга 2 – Москва «Теплотехник», 2004 – 588 с.
- Детков С.П., Еринов А.Е. Тепловые процессы в печных агрегатах алюминиевой промышленности – Киев, «Наукова думка», 1987 – 270 с.
- Монастырев А.В., Александров А.В. Печи для производства извести. Справочник. – Москва, «Металлургия», 1979 – 232 с.
- В.Ф. Першин, В.Г. Однолько, С.В. Першина. Переработка сыпучих материалов в машинах барабанного типа/Москва, "Машиностроение". – 2009. – 142 с.)
- Коротич, В.И. Анализ движения сыпучего материала во вращающемся цилиндрическом барабане / В.И. Коротич // Горный журн., 1964. – № 12. – С. 134 – 141).
- Стаскевич Н.Л., Северинец Г.Н., Вигдорчик Д.Я. Справочник по газоснабжению и использованию газа. – Ленинград, «Недра» Ленинградское отделение, 1990 – 762 с.
- Пат. 47912 Укр., МПК6 F23 D 14/00. Пальник для спалювання газу/ В.С. Пікашов, Л.М. Троценко, С.В. Цвєтков, О.А. Пруський, В.О. Великодний. – Опубл. 25.02.10, Бюл. № 4.
Research Of Influence Of The Shape And Orientation Of The Torch On The Performance Of The Rotary Kiln To Fire Clay Kaolin.
Trotsenko L.N,. Doctor of Technical Science, Pikashov V.S., Doctor of Technical Science, Strativnov E.V.. Doctor of Technical Science, Pravylo S.V., Vynogradova T.V.
The Gas Institute of National Academy of Science of Ukraine
39, Degtjarivska Str., 03113 Kiev, Ukraine, e-mail: t-ln@ukr.net
The Gas Institute of NASU developed and implemented on a rotary kiln for kaolin firing of plant a new heating system based on path gas burner with, 35 MW capacity and with maximum natural gas 4000 m3.Primary air is delivered to burner in an amount of 25-30% of the total required for complete combustion air. Secondary air is delivered through the refrigerator of granular clay by heating to the temperature of 500–700 °C.
Burner is enabled to control the flame length and thereby provide the temperature distribution along the length of the kiln. The flame length control of burner is carried out by means of a gas valve with with holes which can be moved along the axis of burner and partially or fully overlap the main of the gas nozzle. The gas is distributed between the central and lateral holes, making the different conditions for mixing of fuel and air. The distinguishing feature of burner is a fixed in the air gap.
The heating system includes ignition control unit (IGU), safety system and temperature control in the kiln. The nation's first rotary kiln operation to control the temperature in the firing zone in the inner layers of were installed with contactless signal transmission to the control board using wireless modem a solar batteries.
Comparative studies of the influence of the size, shape and orientation of the torch on the heat transfer in the furnace, resulting in the flame, the optimal sizes, the angle of inclination of its axis to the axis of the furnace and its orientation relative to the surface of the heated material. Installation on existing furnaces optimal parameters achieved the following parameters: air flow rate decreased from 1.1-1.3 to 1.05-1.1; is reduced to a vacuum exhaust fan from 1.2-1.5 to 0.8-1.0 kPa, the flow in the natural gas-reduced during continuous operation of the furnace by 30%, and the average fuel economy was 15%.
Keywords: rotary kiln, heating system, the parameters of the flame, heat, masonry.
|